Lean: Unpacking Efficiency, Beyond The 'Beef Patty Ass'
Table of Contents
- The Genesis of Lean: From Toyota's Vision to Global Impact
- What Exactly is "Lean"? Defining the Core Philosophy
- The Five Pillars of Lean: A Framework for Value Creation
- Lean in Practice: Tools, Techniques, and Transformative Results
- Beyond Manufacturing: The Versatility of Lean Thinking
- Lean and Technology: AI's Role in Optimizing Processes
- Addressing Misconceptions: Lean is Not "Mean"
- The Dark Side of "Lean": Understanding "Purple Drank"
- Embracing the Lean Mindset: A Path to Sustainable Success
- Conclusion
The Genesis of Lean: From Toyota's Vision to Global Impact
The story of Lean begins not in a boardroom, but on the factory floors of post-World War II Japan. Toyota, facing resource scarcity and a need to compete with larger, more established Western automakers, developed a revolutionary production system. This system, later dubbed "Lean manufacturing," was originally created by Toyota to eliminate waste and inefficiency in its manufacturing operations. It wasn't just about making cars faster; it was about making them better, with fewer defects, less inventory, and a deeper understanding of customer value. The brilliance of Toyota's approach lay in its relentless focus on identifying and eliminating "muda" (waste), "mura" (unevenness), and "muri" (overburden). This holistic view transformed manufacturing from a series of isolated tasks into an integrated, flowing process. The impact was profound, leading to higher quality products, shorter lead times, and significantly lower costs. This success eventually caught the attention of Western academics and industrialists, leading to its widespread adoption across various sectors.James P. Womack and the Lean Enterprise Institute (LEI)
While Toyota laid the groundwork, it was the work of Western researchers, particularly James P. Womack, Daniel T. Jones, and their colleagues at MIT, that truly brought Lean principles to the global stage. Their seminal book, "The Machine That Changed the World," published in 1990, coined the term "Lean" and meticulously documented Toyota's production system, contrasting it with traditional mass production. To further propagate these transformative ideas, the Lean Enterprise Institute (LEI), founded by James P. Womack, was established. LEI has since become a leading authority in promoting Lean thinking and practices across industries, providing education, research, and practical tools for organizations seeking to adopt this powerful methodology. Their work has been instrumental in demonstrating that Lean is not just a set of tools for manufacturing, but a comprehensive management philosophy applicable to any process or organization.What Exactly is "Lean"? Defining the Core Philosophy
At its core, Lean is a systematic operational method, a way of thinking about creating needed value with fewer resources and less waste. It is defined as a set of management practices to improve efficiency and effectiveness by eliminating waste. The primary goal of Lean is to reduce non-value-added waste in the production process, thereby creating maximum economic value for the customer. In the context of customer consumption of products or services, "value" should be defined as behaviors or actions for which consumers are willing to pay. Lean is founded on two pillars: continuous improvement and respect for people. While often associated with manufacturing, Lean's principles are universally applicable because every organization has processes, and every process can be improved. It's about having the right resources in place to do the right work for the customer, with the right quality, at the right time. Lean allows managers to discover inefficiencies in their organization and deliver better value to customers, moving beyond the superficial notion of simply cutting costs. It's a practice consisting of continuous experimentation to achieve perfect value with zero waste.The Five Pillars of Lean: A Framework for Value Creation
The five Lean principles provide a framework for creating an efficient and effective organization. These principles are not merely steps to follow but a cyclical journey of continuous improvement. Central to Lean is the idea of delivering more value to customers using fewer resources.Value: Defining What Truly Matters
The first and most crucial step in Lean is to precisely define value from the customer's perspective. What is the customer truly willing to pay for? What problem are they trying to solve? Any activity or feature that does not contribute to this defined value is considered waste. For instance, in manufacturing a "lean beef patty," the value is the perfectly cooked, flavorful patty itself, not the time spent waiting for ingredients or correcting errors. Understanding this allows organizations to focus their efforts on what truly matters to the end-user.Value Stream: Mapping the Flow
Once value is defined, the next step is to identify the entire value stream – all the steps, both value-added and non-value-added, required to bring a product or service from raw material to the customer. Value stream mapping is a powerful tool used to visualize this flow, highlighting areas of waste, bottlenecks, and inefficiencies. This comprehensive view helps teams understand how different parts of an organization interact and where improvements can be made. It's about seeing the whole picture, not just isolated processes.Flow: Ensuring Smooth, Uninterrupted Progress
After mapping the value stream, the goal is to make the value-creating steps flow without interruptions, delays, or bottlenecks. This involves reorganizing processes, breaking down silos, and ensuring that work moves smoothly from one step to the next. Achieving flow means eliminating anything that stops or slows down the production or service delivery. This might involve reconfiguring layouts, cross-training employees, or standardizing work procedures. The aim is to achieve a continuous, seamless progression, much like a well-oiled machine.Pull: Producing Only What's Needed
The fourth principle is "pull," meaning that production or service delivery is initiated only when the customer signals a need. This contrasts sharply with "push" systems, where products are made based on forecasts and pushed through the system, often leading to overproduction and excess inventory – significant forms of waste. A pull system ensures that resources are only consumed when there is actual demand, leading to reduced inventory, lower costs, and increased responsiveness. It's about delivering what's needed, when it's needed, and nothing more.Perfection: The Pursuit of Continuous Improvement
The final principle, perfection, emphasizes the ongoing pursuit of continuous improvement. Lean is a continuous process, not a one-time project. Organizations adopting Lean strive for perfection by continuously identifying and eliminating waste, improving quality, and reducing lead times. This involves a culture of problem-solving, experimentation, and learning from mistakes. The journey towards perfection is never-ending, ensuring that an organization remains agile, competitive, and customer-focused. This relentless drive for improvement is what truly sets Lean apart.Lean in Practice: Tools, Techniques, and Transformative Results
Implementing Lean involves a suite of practical tools and techniques designed to support the five principles. These include: * **5S:** A methodology for workplace organization (Sort, Set in Order, Shine, Standardize, Sustain). * **Kanban:** A visual system for managing work as it moves through a process. * **Kaizen:** A philosophy of continuous improvement involving small, incremental changes. * **Poka-Yoke (Mistake-Proofing):** Designing processes to prevent errors from occurring. * **Standardized Work:** Documenting the best way to perform a task to ensure consistency and quality. * **Gemba Walks:** Going to the actual place where work is done to observe and understand processes firsthand. The results of effective Lean implementation can be impressive. Organizations often report significant gains in efficiency, reduced lead times, improved quality, lower costs, and increased customer satisfaction. Lean manufacturing has been around for decades, with implementation of lean tools and techniques resulting in impressive efficiency and production gains. These gains are not just theoretical; they translate directly into bottom-line improvements and a stronger competitive position.Beyond Manufacturing: The Versatility of Lean Thinking
While its roots are in manufacturing, Lean thinking has proven incredibly versatile, finding successful application in virtually every sector. From healthcare to software development, service industries to government agencies, the core principles of value, flow, and waste reduction are universally applicable. In healthcare, Lean helps reduce patient wait times, improve diagnostic accuracy, and streamline administrative processes. In software development, Agile methodologies are deeply influenced by Lean principles, focusing on iterative development, rapid feedback, and delivering customer value incrementally. Even in personal productivity, individuals can apply Lean concepts to manage their time, tasks, and resources more effectively, eliminating personal "waste" and focusing on high-value activities. The power of Lean lies in its adaptability and its fundamental focus on optimizing any process.Lean and Technology: AI's Role in Optimizing Processes
The advent of advanced technologies, particularly Artificial Intelligence (AI) and machine learning, is taking Lean to new heights. Lean is a continuous process, and AI algorithms optimize product movements by constantly analyzing data and making adjustments. AI can process vast amounts of data far more quickly and accurately than humans, identifying patterns of waste and inefficiency that might otherwise go unnoticed. For example, AI can predict equipment failures, optimize inventory levels in real-time, streamline supply chains, and even personalize customer experiences by analyzing demand patterns. This data-driven approach enhances the disciplined, data-oriented nature of Lean. By integrating AI, organizations can achieve even greater levels of precision in waste elimination and value creation, pushing the boundaries of what a truly lean operation can achieve. It allows for dynamic adjustments and continuous optimization that were previously unimaginable.A common misconception, perhaps fueled by the rhyming words, is that "Lean is 'mean'" (although the words rhyme, unfortunately). This couldn't be further from the truth. Lean is not about cutting corners, firing employees, or sacrificing quality to save money. In fact, a core pillar of Lean is "respect for people." A truly lean organization empowers its employees, values their input in problem-solving, and invests in their development. The goal of Lean is to eliminate waste from processes, not to eliminate people. By making processes more efficient, employees are freed from tedious, non-value-added tasks, allowing them to focus on more meaningful and impactful work. This often leads to increased job satisfaction and a more engaged workforce. Lean is about working smarter, not just harder, and building a sustainable, high-performing culture.
The Dark Side of "Lean": Understanding "Purple Drank"
It's crucial to address a starkly different and dangerous interpretation of the word "Lean" that exists outside the realm of business methodology. "Lean or purple drank (known by numerous local and street names) is a polysubstance drink used as a recreational drug." This illicit concoction, also known as sizzurp, barre, and Texas tea, is a mixture of cough syrup, soda, hard candy, and sometimes alcohol. It contains codeine and promethazine, both powerful prescription drugs. This dangerous substance has severe health consequences, including respiratory depression, seizures, and addiction, and has been linked to numerous fatalities. It is imperative to distinguish this harmful street drug from the legitimate and beneficial management philosophy of Lean. The two concepts share only a word in common and are otherwise entirely unrelated in their meaning, purpose, or impact.Embracing the Lean Mindset: A Path to Sustainable Success
Embracing Lean is not merely about adopting a set of tools; it's about cultivating a mindset. It's a way of thinking that constantly questions the status quo, seeks out waste, and strives for continuous improvement. This disciplined approach leads to organizations that are more agile, resilient, and better equipped to meet evolving customer demands. For any organization, big or small, the journey towards becoming truly lean is a strategic imperative in today's competitive landscape. It requires commitment from leadership, engagement from all employees, and a willingness to challenge established norms. The rewards, however, are substantial: increased quality, lower costs, faster delivery, and ultimately, greater value for the customer. It's about building an operation so streamlined and efficient that it operates with the precision of a finely tuned machine, leaving no room for the metaphorical 'ass'ets of waste.Conclusion
From its origins at Toyota to its widespread adoption across diverse industries, Lean has proven to be a powerful, transformative methodology. It's a set of management practices that produces value for customers quickly through a focus on reducing delays and eliminating waste, which results in increased quality and lower cost. While the phrase "lean beef patty ass" might be a whimsical way to think about optimization, the true essence of Lean is a rigorous, data-driven pursuit of perfection, centered on delivering maximum value with minimum resources. By applying the five Lean principles – defining value, mapping the value stream, creating flow, establishing pull, and pursuing perfection – organizations can unlock unprecedented levels of efficiency and effectiveness. If your organization is struggling with inefficiencies, high costs, or customer dissatisfaction, exploring Lean principles could be the transformative solution you need. We encourage you to delve deeper into Lean resources, perhaps starting with the Lean Enterprise Institute, and consider how these timeless principles can revolutionize your operations. Share your thoughts in the comments below – how do you envision a "lean" future for your business?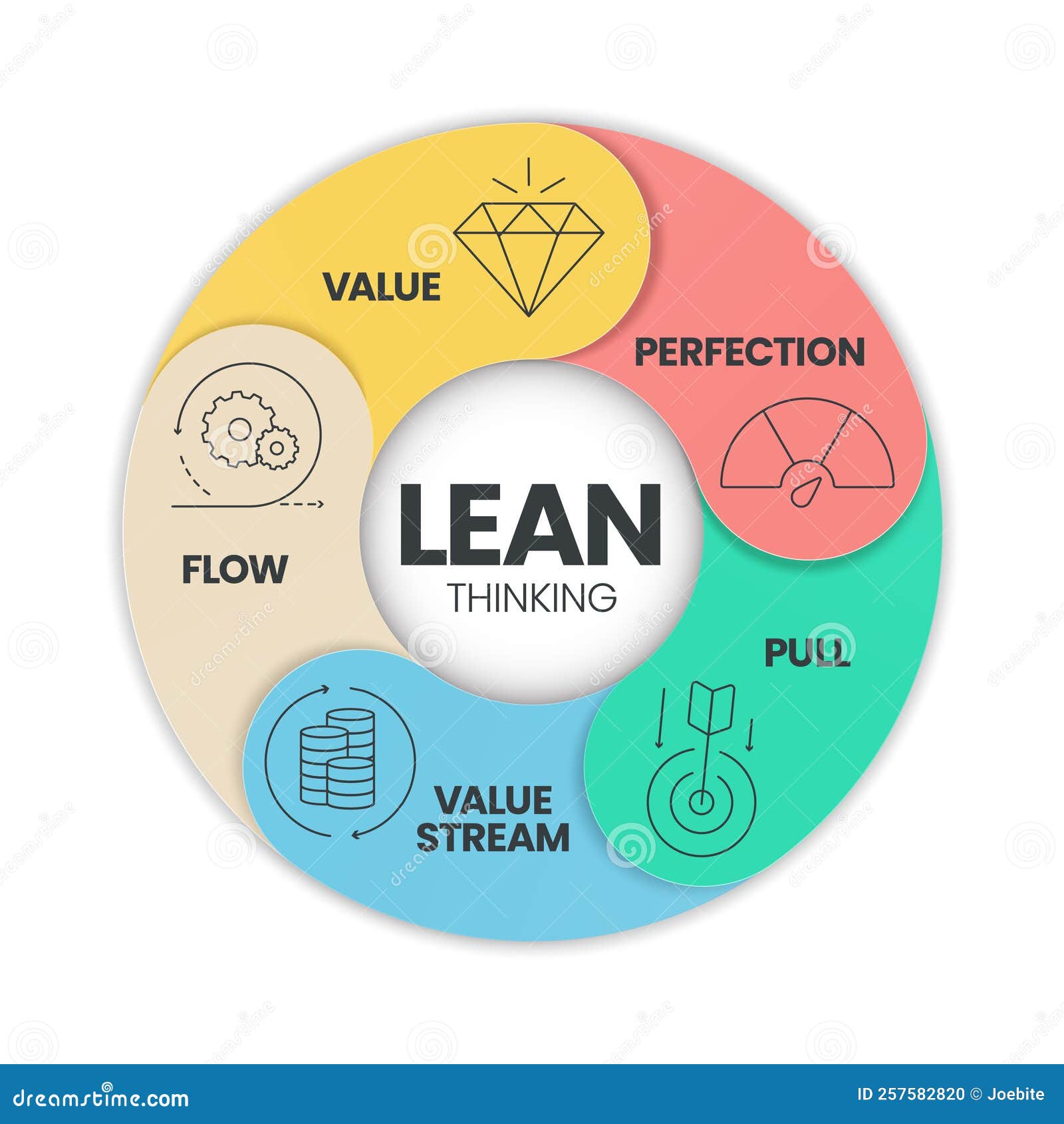
LEAN Thinking Diagram Infographic Template with Icon Has 5 Steps To
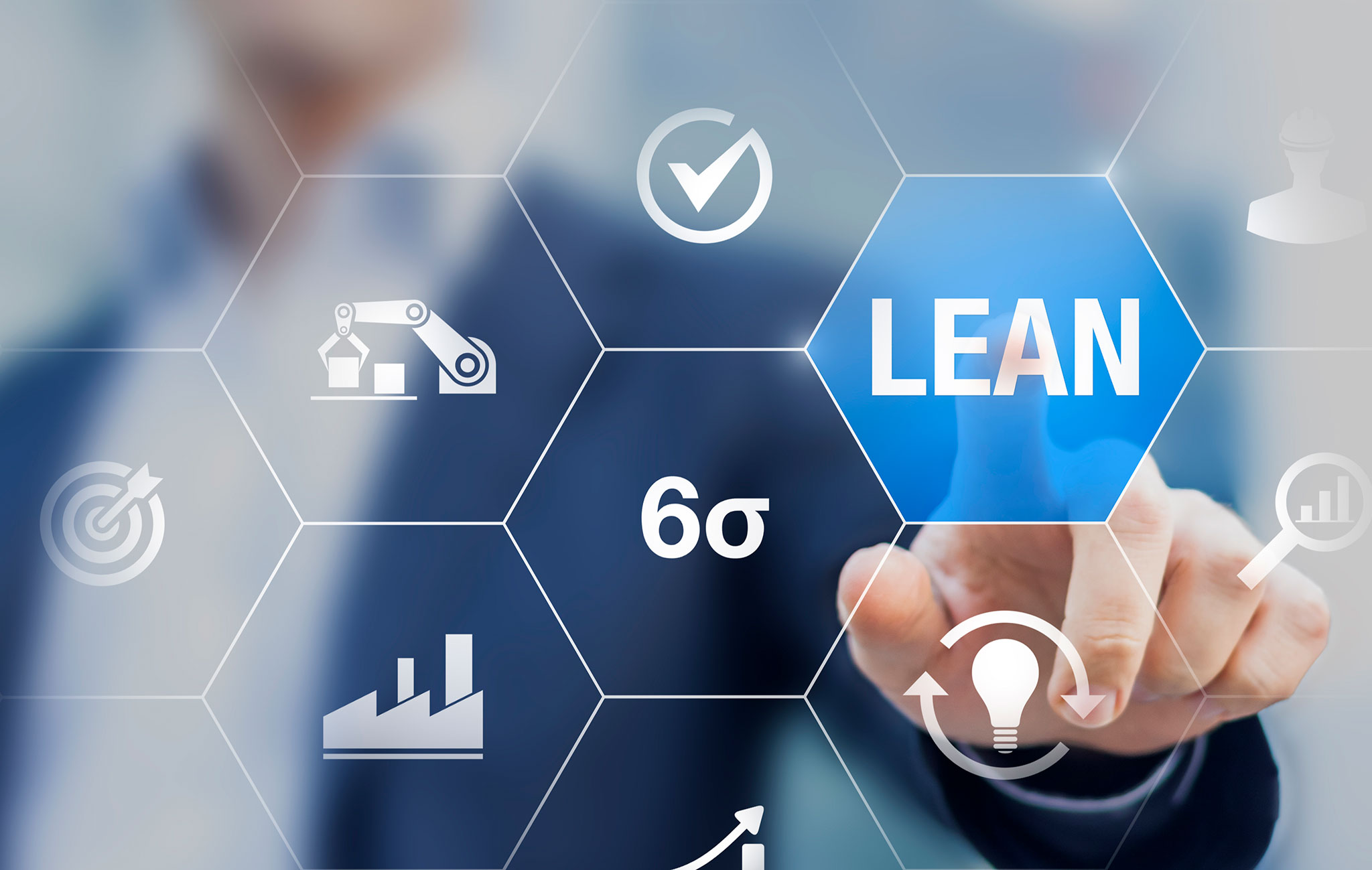
What is Lean Manufacturing and the 5 Principles Used? - TWI
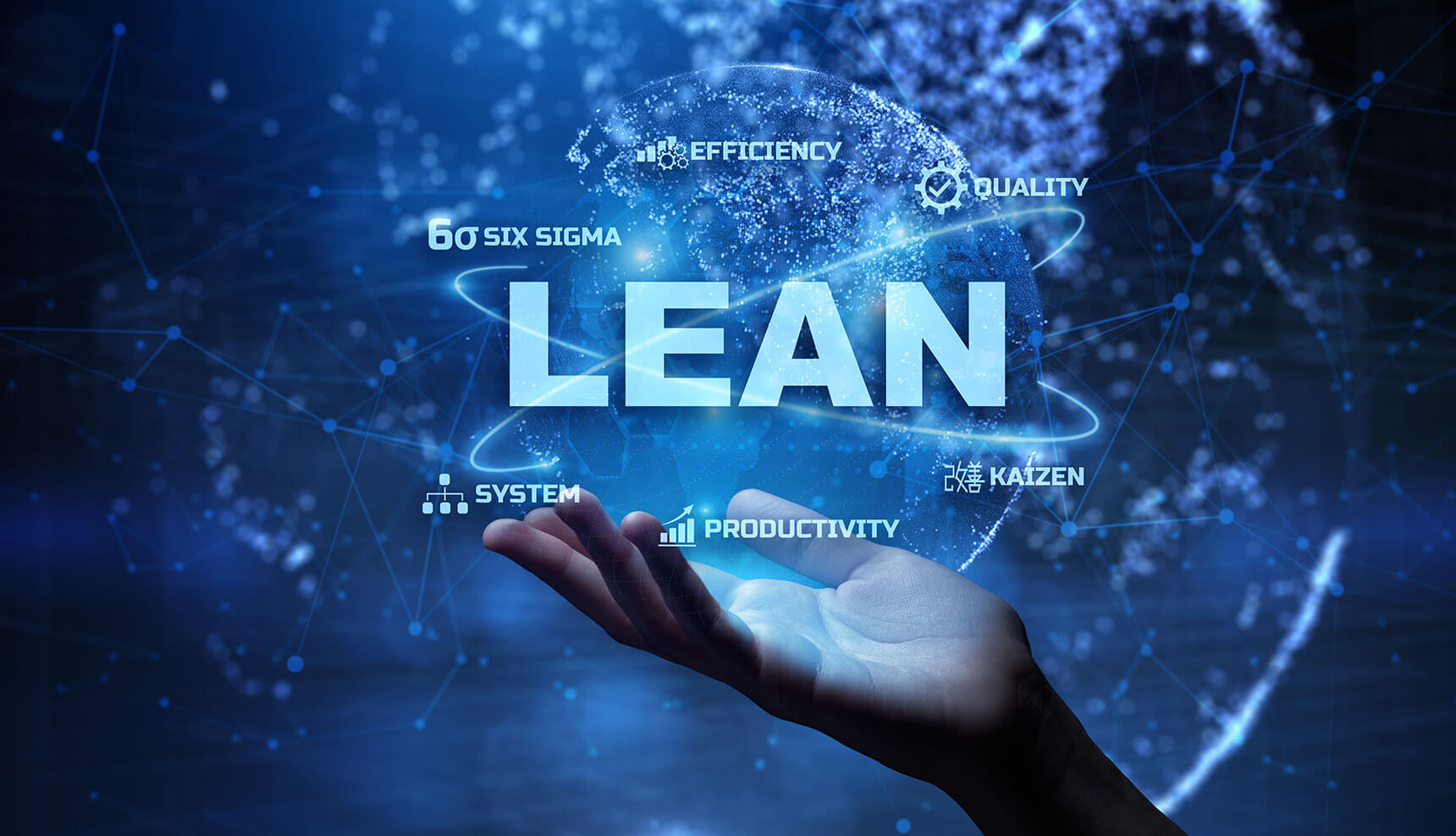
Lean Research – Is Lean a Theory? - #SINTEFblog